The logistics service provider FIEGE relies on an integrated system solution from Element Logic for small parts storage, warehouse management and process control at its logistics center in Apfelstädt. With one of the largest AutoStore systems in Germany and the SuPCIS-L8 warehouse management system from S&P, process efficiency has reached a new level. The successful implementation of this major project optimizes order production for the omnichannel business, increases flexibility and offers long-term investment security as well as a solid basis for further growth.
The figures are impressive: The family-run company FIEGE from Greven in Westphalia operates one of its mega centers on an 80,000 square metre site in Apfelstädt. The contract service provider has been based at the multi-user logistics center southwest of Erfurt since 1994. Products for various customers are stored there, picked and shipped to customers throughout Europe. Since 2014, FIEGE has been handling warehousing, Germany-wide store distribution, e-commerce fulfillment and returns management as well as B2C parcel shipping within Germany, to Austria and Switzerland for a sporting goods retailer in Apfelstädt. Around 140,000 SKUs are stored and processed at the FIEGE site in Apfelstädt.
"The increasing importance of the successfully growing e-commerce business has significantly increased the demands on internal throughput times," explains Frank Maron, Senior Logistics Consultant at FIEGE. "Against this backdrop and thanks to a predictable contract term, we have restructured the warehouse logistics business for our long-standing customer at the Apfelstädt site and integrated more efficient automation processes."
Decision for AutoStore
Due to planned changes to order structures, FIEGE has reorganized the coordinated process control with a modern warehouse management system and the small parts storage processes in addition to several conveyor technology connections. After several system comparisons, FIEGE decided to install a state-of-the-art AutoStore cube.
"In the fast-moving omnichannel business, maximum availability of goods and minimum throughput times are important success factors," emphasizes Frank Maron. "The Autostore system offers an integrated and scalable system that meets these requirements. It provides us with more storage capacity in a significantly smaller space and reduces the manual picking effort to a minimum. This speeds up the overall warehouse throughput time considerably."
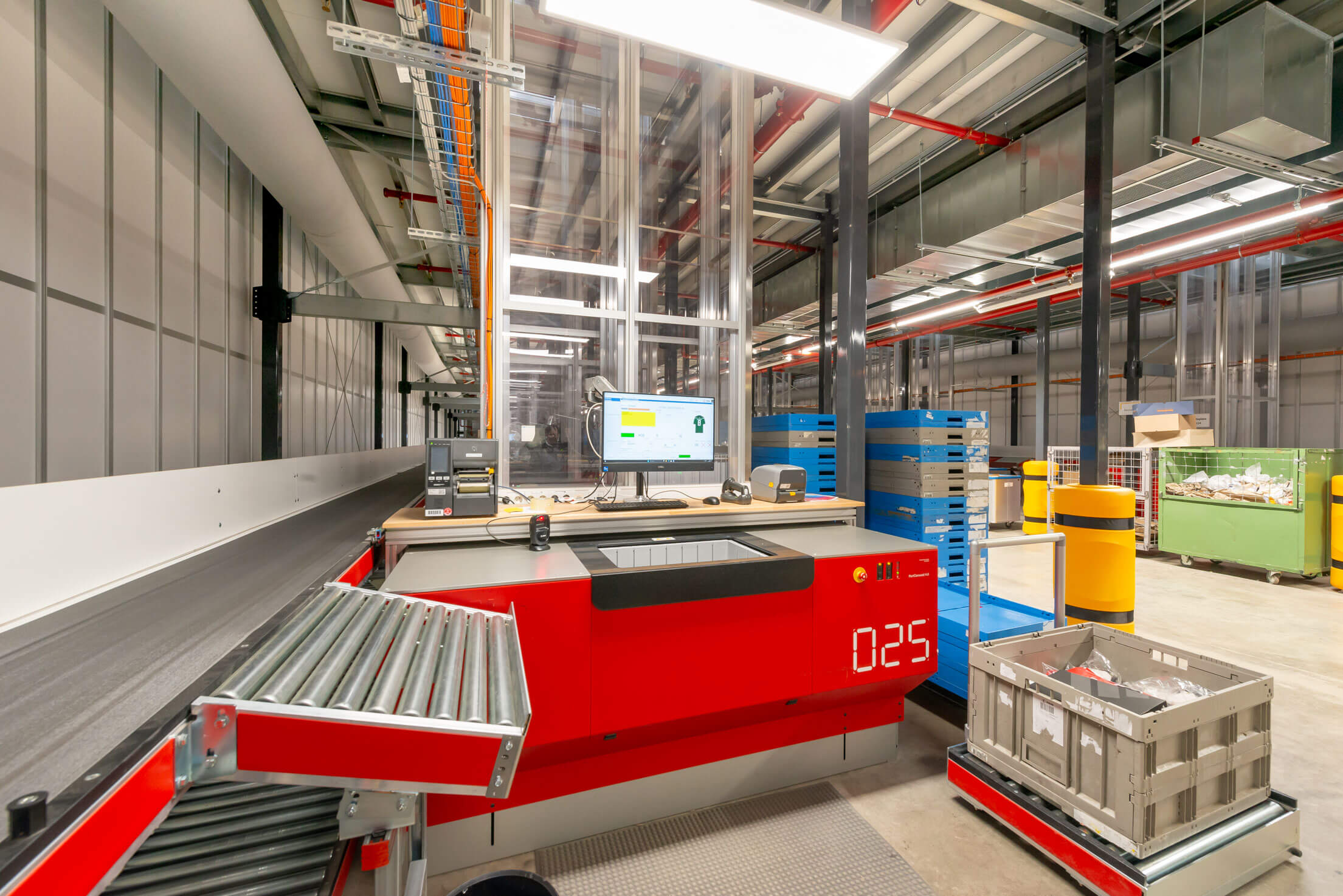
First jointly realized solution with S&P
The contract for system design and project implementation was awarded to Element Logic, the world's first AutoStore integrator. "Proven expertise and impressive reference systems were decisive factors in the award of the contract," explains Maron. "In addition, Element Logic had extensive conveyor technology expertise and, with its subsidiary S&P, a software provider with a proven warehouse management system in its product portfolio. This allowed us to plan for a comprehensive, integrated solution and a harmonious, coordinated project process."
The successful large-scale project at FIEGE is the first solution that system integrator Element Logic has implemented together with the software experts from S&P, who have been part of the Element Logic Group since the end of 2022. "The successful course of the project shows how well the two companies complement each other with their expertise and specifications in order to develop and implement an optimal solution for the customer," says Joachim Kieninger, Director Strategic Business Development at Element Logic Germany.
One AutoStore system in two halls
With the AutoStore system from Element Logic, FIEGE is implementing a pioneering automation project for its customer in the Apfelstädt multi-user center. On a floor area of almost 10,000 square meters, Element Logic is creating an AutoStore system in Germany that is as large as a soccer pitch. The system's storage grid offers space for 270,000 bin storage locations. Special feature: thanks to the adaptability of the system components, the system could be flexibly installed in two separate hall areas in terms of fire protection. Fire protection doors were also integrated into the grid. This allows the flexible use of 160 R5 robots in both hall areas. The robots work on the grid surface of the system and take over the storage, retrieval and transfer of the containers across the hall separation.
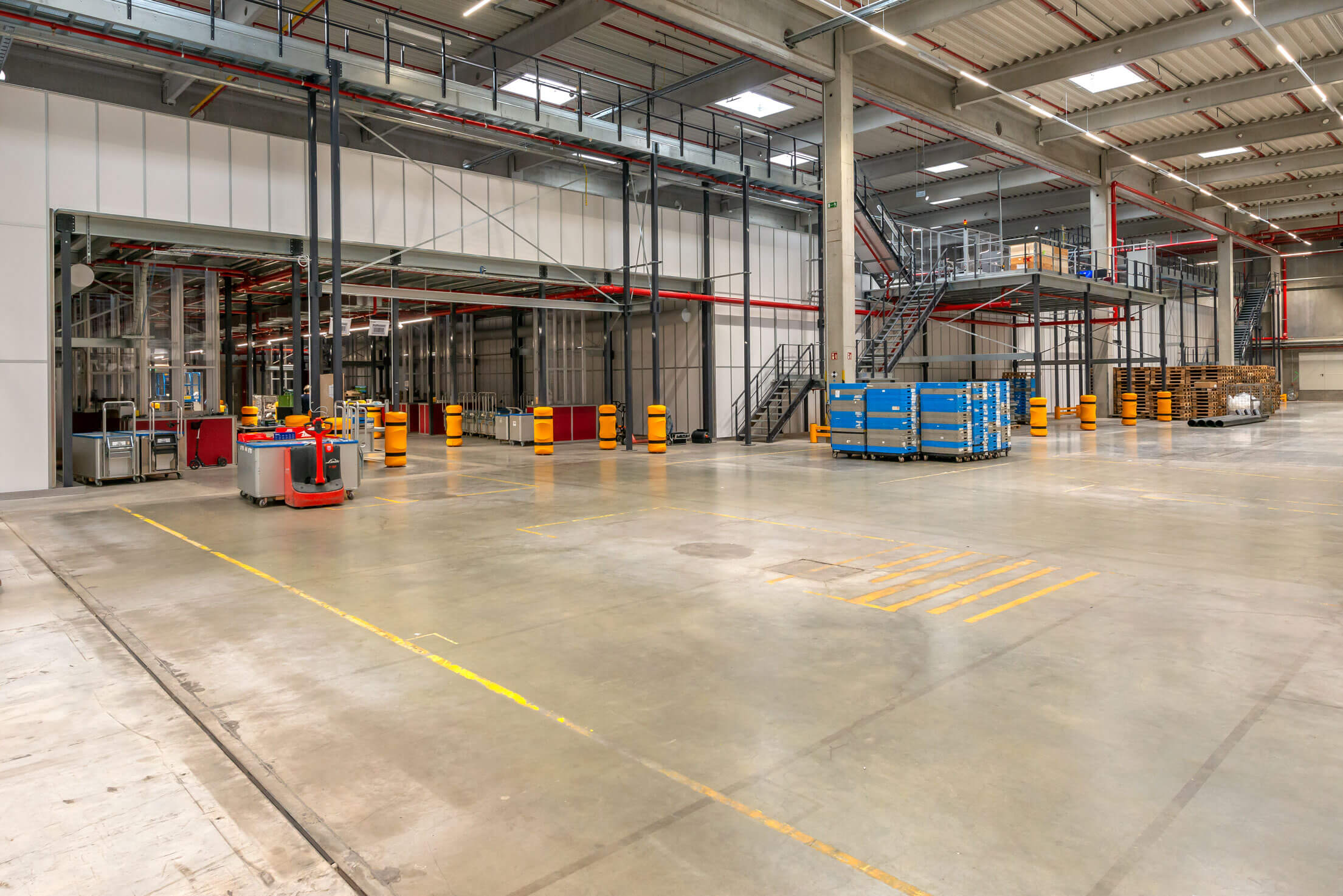
For order picking, the robots store the containers at picking stations, known as ports. These are arranged in a tunnel that is integrated into the system. The system comprises a total of 28 carousel ports, which are designed for high throughput rates and are part of the modular AutoStore system. The material flow software eController from Element Logic is used for process control. In addition, Element Logic has integrated four transfer cells with conveyor technology into the system design for the goods storage processes. They connect the AutoStore system with the repacking stations in the incoming goods area and also handle the supply of empty containers. "The system concept is designed for process efficiency and flexibility, making it the ideal system for FIEGE to meet the omnichannel requirements of its customers," explains Kieninger. "We also support FIEGE during operation with a comprehensive after-sales service package to jointly ensure high system availability."
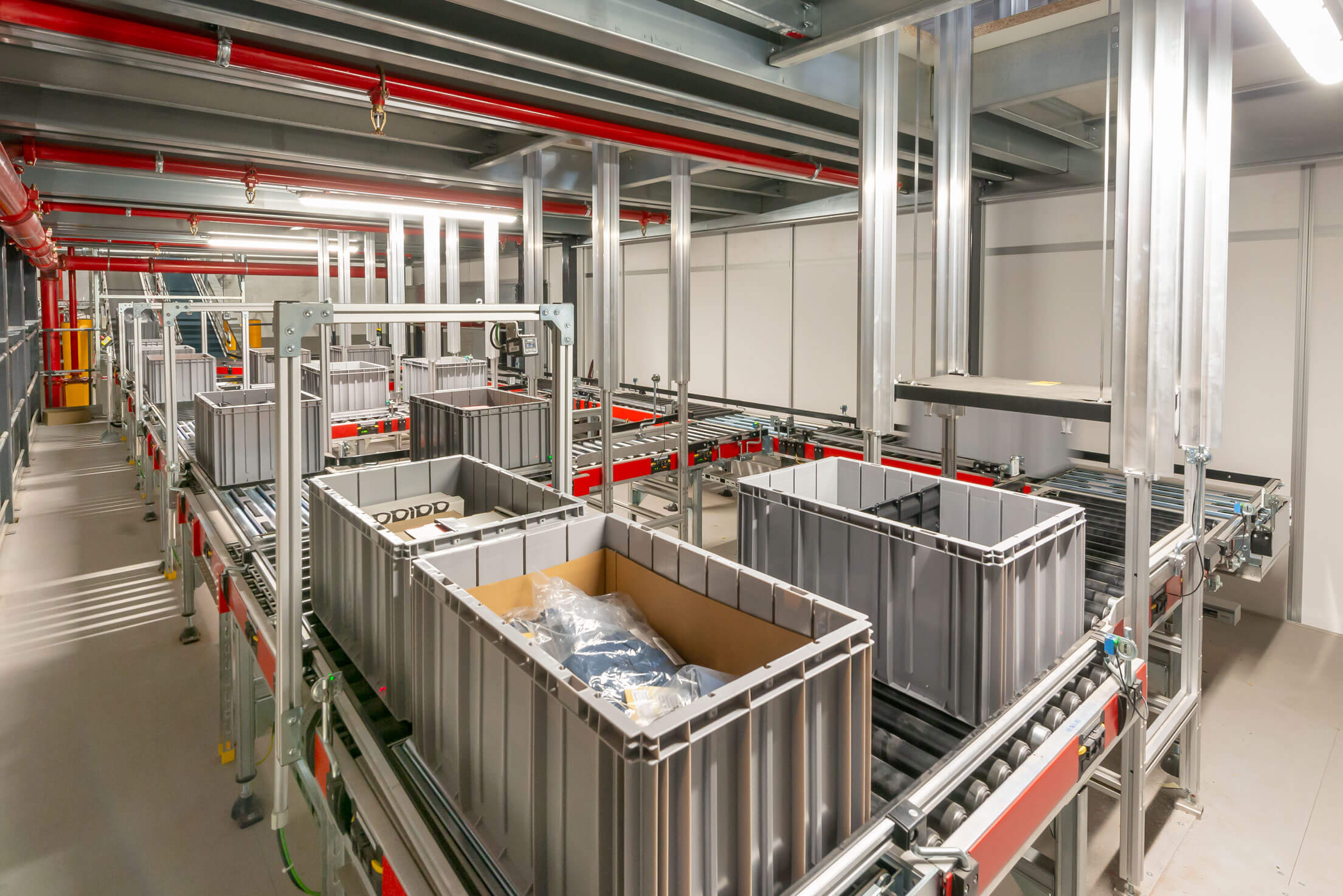
WMS for maximum flexibility
FIEGE decided to implement the tried and tested SuPCIS-L8 warehouse management system (WMS) from S&P to control the complex order processing processes at the Apfelstädt logistics center. What is striking in this context is that the WMS connects the AutoStore system to the coordinated process control via a standardized interface, the AutoStore Connector. SuPCIS-L8 thus takes over inventory management as well as material flow and process control. The eController from Element Logic controls the transfer cells and in this way links the container conveyor technology from the incoming goods department with the AutoStore system. Both the eController and SuPCIS-L8 are connected to Element Logic's eHub communication platform. Other existing system components from other suppliers are also connected to the eHub. In their first major joint project, Element Logic and S&P are thus already delivering a modular and easily expandable platform on the software side, which is presented to customers in a standardized way and can be fully integrated.
The WMS manages the stocks in the AutoStore warehouse, requests the articles on an order-related basis, sequences them from the container warehouse and controls the dialogs of the connected workstations. "With FIEGE, the project involves a demanding customer who expects maximum flexibility from the WMS," states S&P Managing Director Rémy El Abd. "For the FIEGE customer, this is aimed in particular at controlling fast, efficient order processing; for FIEGE, above all, at convenient adaptability of the system and easy control of the multi-user site with simple onboarding of additional customers. Our WMS SuPCIS-L8 fulfills all these requirements."
Multi-client capable system design
FIEGE had diverse and demanding requirements for the WMS. These ranged from strategic reservation for various order types and central workstation control in the control station to the reorganization of container management. "Thanks to its design and size, the AutoStore system at FIEGE in Apfelstädt enables a level of processing that has not yet been realized in the AutoStore environment," adds Ferdinand Gantert, Team Lead Product at S&P.
"In order to fully exploit this potential and take into account some of the special features of the fashion industry, we were able to implement several software features in close cooperation with the experienced logistics experts at FIEGE, which are completely new for AutoStore systems and open up completely new possibilities for the user."
In terms of true multi-client capability, FIEGE can, for example, use the same article number for different customers and keep it in separate stocks, carry out user-specific configurations independently and store different process sequences for different customers. Optimized returns handling of mixed containers is also possible, as well as - for greater reliability in the picking process - an EAN scan for article counting at the port or task-specific packaging processes after the last picking. The system's multi-client capability enables FIEGE to easily integrate new customers in the future and manage their different warehouse processes. In addition, SuPCIS-L8 coordinates the consolidation and order processes. "With the scalability of SuPCIS-L8, FIEGE is on the safe side in terms of guaranteed long-term flexibility," adds Joshua Smith, Director Delivery & Customer Success at S&P. "Our developers can add new functions quickly and easily at any time via configurations. In this way, FIEGE can continuously optimize processes and seamlessly integrate additional locations or manual warehouses into the system. The software therefore supports FIEGE's growing requirements."
Ideally equipped for future challenges
The AutoStore system and the WMS have now been implemented at the logistics center in Apfelstädt and have already proven their worth in day-to-day operations. The integrated automation solution supports the employees there with efficient, reliable order processing and makes a significant contribution to simplifying processes and saving time. "All hardware components and the software of the overall solution are scalable as demand grows, increasing flexibility and offering FIEGE long-term investment security," summarizes Kieninger. "The system will take the service for FIEGE's customers and consignees to a whole new level. FIEGE is therefore ideally equipped for future challenges."
More details on the software requirements and software features relating to AutoStore: Read now!
If you want to see what it looks like in practice at FIEGE, click here: Watch the movie!