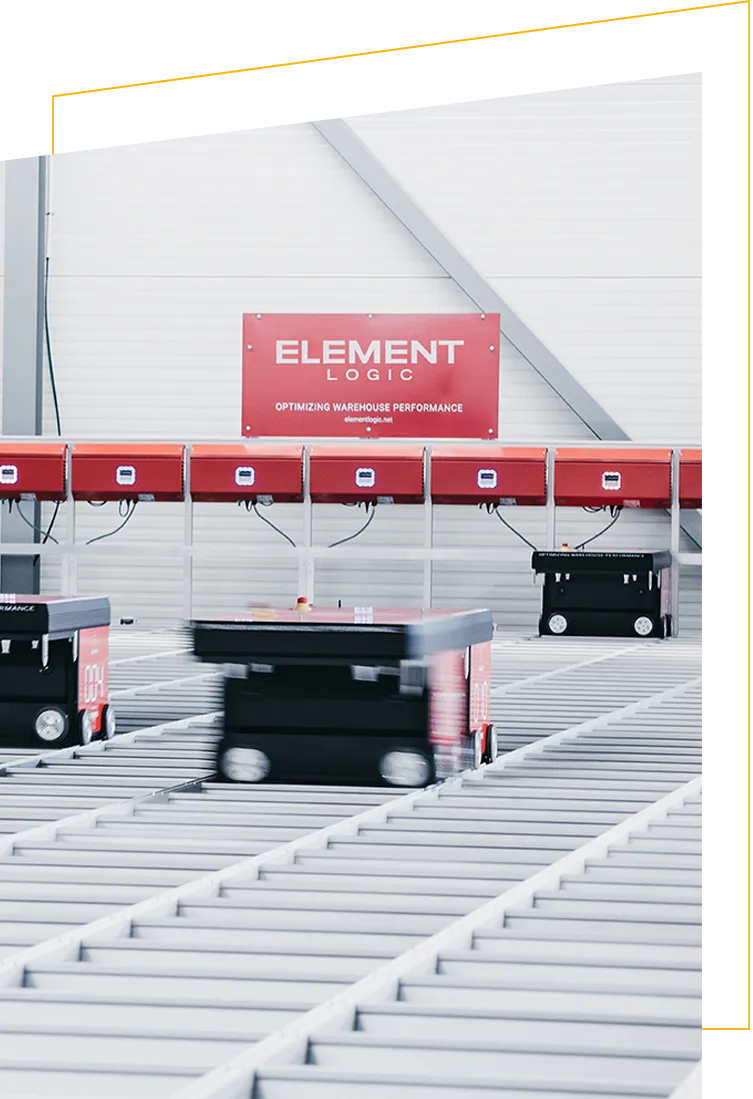
Innovative storage technology in the smallest space
What is AutoStore®?
AutoStore® is a goods-to-person system that knows neither aisles nor shelves. It uses almost the entire floor space for storage. It therefore offers up to four times the storage capacity of a manual warehouse. Conversely, this means significantly more space for your product range.
This means that larger storage capacities can be achieved even in the smallest of spaces. The integration of an AutoStore® is ideally suited for companies whose storage capacities can hardly be expanded and storage space is limited.
Thanks to its flexibility and modularity, it can be easily expanded during operation. The AutoStore® can be perfectly adapted to your operational and structural conditions if your current system has become too small.
The next generation of warehouse automation
Advantages of the solution
AutoStore® combines everything that customers want in today's world. Reliably manage their stock levels, keep delivery promises and keep an eye on costs at the same time.
Space-saving
Reduces space requirements by 75 % compared to other storage systems.
Reliable
The technology is easy to maintain and offers an uptime of 99.7 %.
Expandable
The aluminum scaffolding is easy to assemble and extend.
Sustainable
No need for light and the robots require very little energy.