With its motto: "It's that easy", KRAMP has taken a successful position in the market as Europe's leading wholesaler of spare parts and accessories for agriculture, forestry and gardening, and construction machinery. Since its foundation in 1951, KRAMP has now successfully pursued the goal of making work as easy as possible for its customers through its product portfolio - from chainsaws and hedge trimmers to accessories for forestry and landscape maintenance and spare parts. In order to remain a reliable partner of the specialized trade in the future and as a company to always be able to offer its customers the best possible service, KRAMP has decided to modernize and expand its warehouse logistics worldwide - at its locations in Germany, England, France, Italy, the Netherlands, Poland and Spain - and has since been a long-standing customer of S&P Computersysteme GmbH.
Over the years, what started in 2007 has not only developed into a close and trusting cooperation between the KRAMP Group and S&P, but also into an impressive growth story. Together, the two project partners continue to tread the path towards the future and work continuously on innovative enhancements to the current system. The WMS (Warehouse Management System) SuPCIS-L8 contributes to an increase in efficiency through an optimized material flow in the warehouse, both in Germany and at the other locations.
In order to cope with the growth of recent years and to replace the existing distribution warehouse, KRAMP decided in the summer of 2007 to build a new central warehouse in Strullendorf near Bamberg in Bavaria and to introduce the SuPCIS-L8 warehouse management software there (for the first time). The new logistics center, planned by IWL AG, an engineering firm for plant planning and logistics in Ulm, has become the hub of all the company's logistics activities in Germany. A large number of specialist dealers for agricultural machinery and motorized equipment are supplied from Strullendorf. The company headquarters and also the service center of the KRAMP Group are located in the Netherlands.
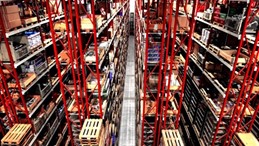
Optimized intralogistics through a customized overall solution
With more than 30,000 square meters of space, the warehouse complex at the Strullendorf site offers 25,000 pallet spaces, a three-story pedestal rack system with 235,000 storage spaces, and other storage areas sufficient space for KRAMP's diverse product range. Within the existing IT landscape of best-of-breed solutions, the warehouse management system SuPCIS-L8 by S&P takes over the control of all intralogistic workflows and processes in the warehouse, from goods receipt to picking, consolidation and packaging. In addition, SuPCIS-L8 is connected to the control of the conveyor technology for the shuttle of KNAPP AG as well as for the areas of the multi-level shelf system, also from KNAPP.
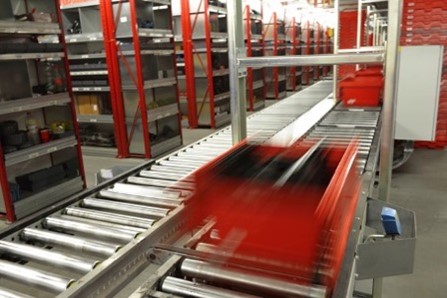
"The possibilities available to us through the introduction of S&P's warehouse management software already became clear during the development of the intralogistics concept: efficient and clear processes for a smooth material flow. Due to the flexibility and scalability of the software, we will also be able to make future-oriented adjustments to the current system and are thus prepared for the dynamic market requirements of our customers," explains Siegfried Gößwein, Logistics Director at KRAMP.
The numerous products and goods arrive at KRAMP's warehouse via the goods receiving area and are then separated by the employees. A special feature of the goods receipt process is the priority-controlled goods receipt buffer warehouse. Here, stocks are buffered briefly after arrival at the goods receiving area in order to cushion peaks in internal processing and ensure a smooth picking process.
In addition, SuPCIS-L8 also handles workshop order processing (assembly and production). In addition to the products specially manufactured at the customer's request, KRAMP produces items in the factory's own workshop as a stock reserve, which are buffered in the warehouse after completion. The individual order data can be viewed at any time via the system. At the same time, employees can post the manufacturing times and costs directly to the customer order number in the WMS, thus recording the scope of the service as an extra service. Finally, the respective order can be invoiced and the printing of the workshop papers initiated. In order to have a complete overview, the process of electronic data interchange (EDI) in goods receipt was consequently also integrated into the WMS. In this way, the communication processes for managing and checking all replenishment processes of articles and stocks between the individual locations take place. The paperless processes simplify workflows and provide a transparent overview in real time.
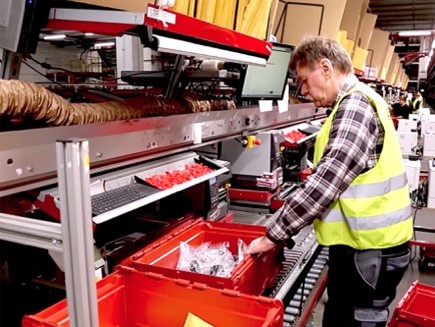
The switch to automatic selection of the picking type (time and picking-dependent) forms the basis for route-optimized and efficient picking. Consolidation strategies that meet KRAMP's requirements ensure a sensible combination of the delivery items to be delivered throughout the picking process. The use of MDEs with mobile printers also makes it possible to mark the goods and apply shipping labels to the packages ready for shipment during picking, thus reducing both the time spent at the packing station and the packaging material required. Another typical industry requirement is the management of remaining lengths for yard goods. Here, too, the WMS provides support and offers a transparent insight into the available stocks in the warehouse at all times. All in all, the introduction of SuPCIS-L8 has raised efficiency in the warehouse to a new level and created a modern and transparent warehouse management system.
Realizing visions - consistent continuation of the modernization and expansion strategy
Growing does not mean becoming as large as possible as quickly as possible, but rather (re)designing the conditions in such a way that the processes remain efficient and scalable in the long term. Thus, after the successful go-live at the Strullendorf site, the KRAMP Group has decided in recent years to significantly expand and modernize its logistics structures. In 2009, S&P's WMS was put into operation at the existing warehouse complex in Varsseveld (Netherlands) and at the site in Biggleswade (England). In 2012, the system went live in Poitiers (France) and in 2015, the SuPCIS-L8 warehouse management software went live in Konin (Poland). Since 2016, the SuPCIS-L8 WMS has ensured the best possible flow of goods in the logistics center at the Madrid site (Spain). In 2018, the system was introduced in Reggio Emilia (Italy) and since then has also enabled smooth and transparent processes in the warehouse here. More locations have been added in the recent past. In 2020, for example, KRAMP decided to open a new location in England and to introduce the SuPCIS-L8 logistics software there. With the go-live in March 2021 in the new warehouse in Spain and July 2021 in Italy, the system from S&P was integrated in two further locations and is also responsible for an optimal material flow in the warehouse there.
"I have been supporting our customer KRAMP for many years now and was able to witness the entrepreneurial growth with my own eyes. The cross-national implementation of the warehouse management software required careful analysis each time. This is because each location differs in parts with regard to warehouse technology and has additional country-specific requirements and challenges that had to be taken into account and overcome," says Rolf Kienzle, Senior Project Manager at S&P.
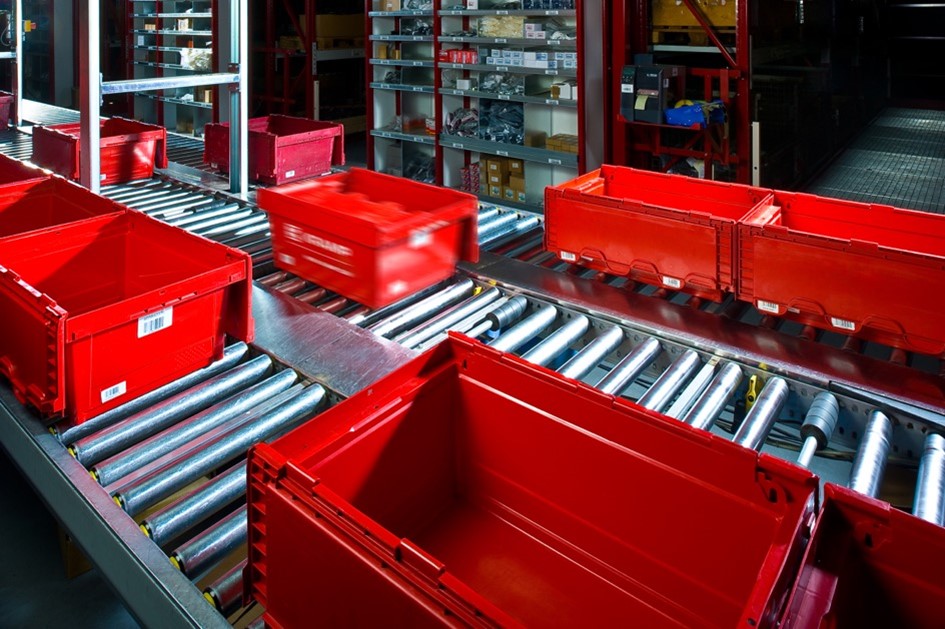
When designing the warehouse strategies, the two project partners focused on largely similar processes in the warehouse. Processes and strategies that are used with the WMS SuPCIS-L8 in Germany can also be found in the other warehouse locations. For example, the management of workshop processing has not only been integrated into the logistics concept in Germany, but also increases the level of service KRAMP provides to its customers in the Netherlands and France. In addition, the system presents important information for control in the warehouse clearly and compactly in dashboards and reports at the individual locations worldwide. The management of blister production can be found in France as well as in the Netherlands.
The connection of SuPCIS-L8 to the control of the conveyor technology for the shuttle of KNAPP AG is used in Germany and the Netherlands - trouble-free extensions during operation are possible here at any time. The KRAMP Group also relies on the WMS from S&P at its own service center in Varsseveld (Netherlands). Here, the warehouse management software SuPCIS-L8 supports the workshop order processing of the assembly and production for the products, which are mostly specially manufactured according to the customer's request - from articles from the hydraulics sector to products made of steel to the specially manufactured electrical appliances. The Warehouse Management System is used to plan the picking of the individual items needed to manufacture the customer-specific products - the individual order data can be viewed in the system at any time. At the same time, the employees in the WMS post the activities, manufacturing times and costs directly to the sales order number and thus have the possibility to process the orders in a structured and transparent manner.
S&P's scalable and flexible software solution SuPCIS-L8 enables the KRAMP Group worldwide to optimally utilize and manage its intralogistics. With intelligent processes and workflows, the efficiency at the warehouse locations could be increased and a modern warehouse management could be created across countries. "When it came to choosing the right partner, we decided on S&P many years ago and placed our full trust in our project partner. Due to the cross-national implementation of SuPCIS-L8 and the individually coordinated processes in the warehouse we have since then a state of the art intralogistics and see ourselves also in the long term able to cope with the growing customer requirements in a dynamic market environment and to manage the logistic processes in the best possible way. I am looking forward to further successful cooperation and the introduction of SuPCIS-L8 in other countries," says Martijn Bonte, COO of the KRAMP Group.