The owner-managed German specialist for electrotechnical solutions JÄGER DIREKT has placed its full trust in the implementation of the warehouse management software SuPCIS-L8 from S&P Computersysteme GmbH at its electrical factory in Heppenheim. Since its opening in summer 2016, the warehouse complex at the Heppenheim site combines the areas of logistics and production. By combining these two areas and implementing an efficient and automated logistics strategy, JÄGER has since been able to react even faster to customer requests and reduce delivery times in the best possible way.
True to the motto: "Inspire people together with heart and soul", JÄGER has set itself the goal of growing steadily through and with the success of its customers. The warehouse complex offers sufficient space for the wide range of products - from the produced quality brands OPUS® switch ranges and Smart Home, DELUNA® recessed spotlights to the VOTHA® wall-mounted distributors and the JUMBO® cable drums and SIROX® mobile power supply. This assortment is completed by many other trade goods of well-known manufacturers.
In order to meet the constant challenges in the long term, the two project partners focused on smooth and efficient processes for incoming goods through picking and production supply to shipping. "During the search for a suitable project partner, it was quickly clear to us that we would choose S&P Computersysteme GmbH and the flexible WMS SuPCIS-L8. Already at the beginning of the joint project it became clear that our requirements for the logistic processes would be implemented in the best possible way and that we can count on further growth in the future due to the flexibility of the solution", says Jochen Schirmer, logistics manager at JÄGER.
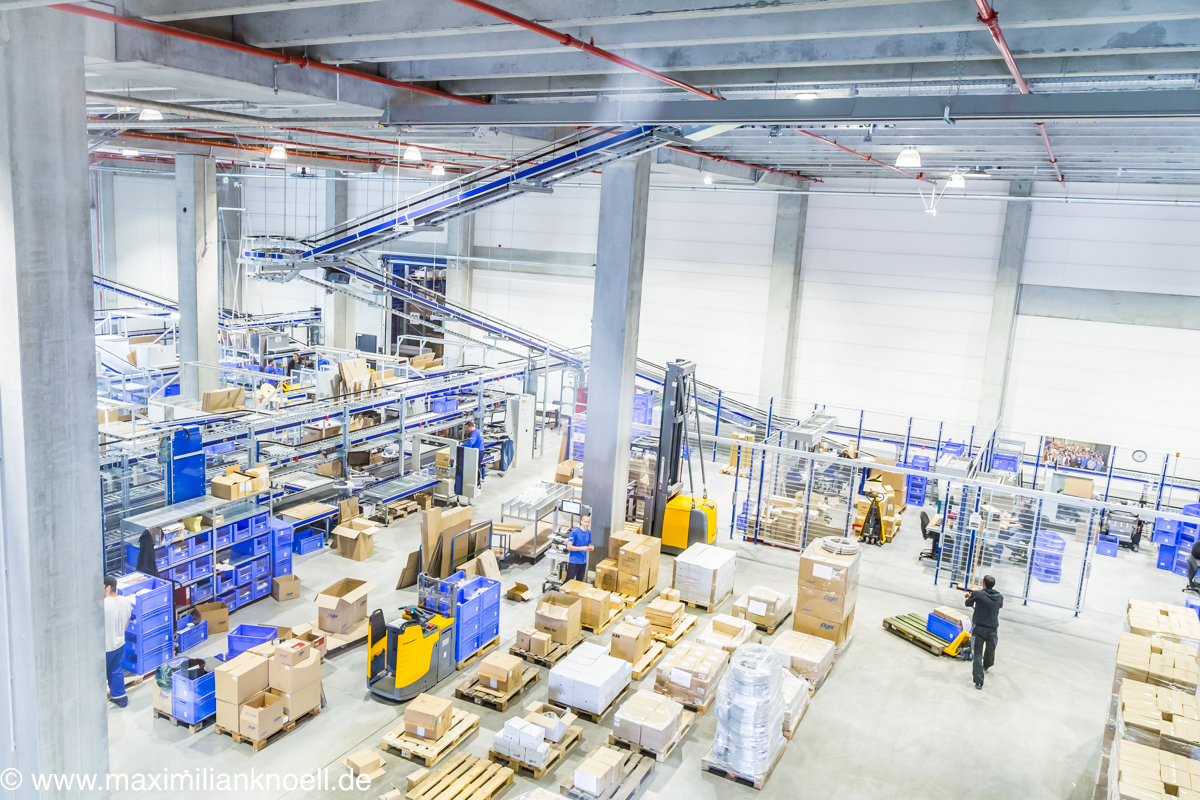
For the design and realization of the plant, JÄGER placed its trust in the planning office Maier Intraplan GmbH and was thus able to draw on the experience and expertise of Hans-Joachim Maier.
Efficientmaterial flow in the warehouse
The control and management of all logistical processes is handled by the powerful SuPCIS-L8 warehouse management software. In addition, integration with the Microsoft Dynamics NAV ERP system enables the WMS to provide information on order progress and the current inventory situation in real time. In order to make the best possible use of the existing potential in terms of transparency, efficiency and benefits in the warehouse, JÄGER deliberately opted for automation. Through the seamless interaction of the WMS SuPCIS-L8 and the MFC (Material Flow Controller) with the system controls of GEBHARDT Fördertechnik GmbH, the electrical wholesaler benefits from a customized and efficient material flow.
The responsible project manager Gerd Müller (Senior Project Manager at S&P Computersysteme GmbH) continues: "Due to the fact that it is a new building, it was, as they say, a planning "on the green field". Working in partnership, we were able to meet the individual requirements of logistics and production in the best possible way and plan the logistical processes. After all, combining these two areas also means taking into account the interlocking processes in the system and integrating them into the overall process in the best possible way."
Fast and transparent logistics processes
The numerous deliveries, such as finished goods from production, external supplier orders and customer returns, arrive at JÄGER via the goods receiving area, are separated there by the employees and it is determined in which storage area the goods are to be stored. The transfer of incoming orders or order data to the WMS takes place permanently. Customer orders are entered in the system and transmitted to the WMS in the form of a picking slip without an availability check and created there as a picking order. JÄGER uses totes, pallets and cartons for picking goods. In the shelf storage system, picking is route-optimized, in totes and with the use of picking carts. After completion of the picking process, the totes are delivered to the conveyor system. If further picks are open for the respective order, another transfer order is created with the remaining target stations to be approached in the picking carousel. The software decides at which target station the totes can be discharged next. Once the tote has been completed, a transport of the totes is generated either to the outgoing goods buffer or directly to one of the ten packing stations. Picking for piece goods takes place in the pallet warehouse. The goods are staged here in the general cargo shipping area and staged in an order-related storage bin in the shipping area for general cargo.
Smooth production processes
To ensure an efficient logistics strategy at the Heppenheim site, the in-house production of WERK 28 GmbH & Co. KG, a subsidiary of JÄGER, was integrated into the logistics process. In addition to stock goods, customer-related products are also produced in this production area: At JÄGER (WERK 28), customer-related means that the individual devices, modules and assemblies are prefabricated in the factory specifically for the customer's requirements so that they can install the product directly. In order to achieve the best possible supply to production at this point for the manufacture of the goods, material provision for production is supported by the WMS SuPCIS-L8. Information is also exchanged via the interface between the WMS and the ERP system, thus creating a transparent and up-to-date overview of the inventory situation in the warehouse and production.
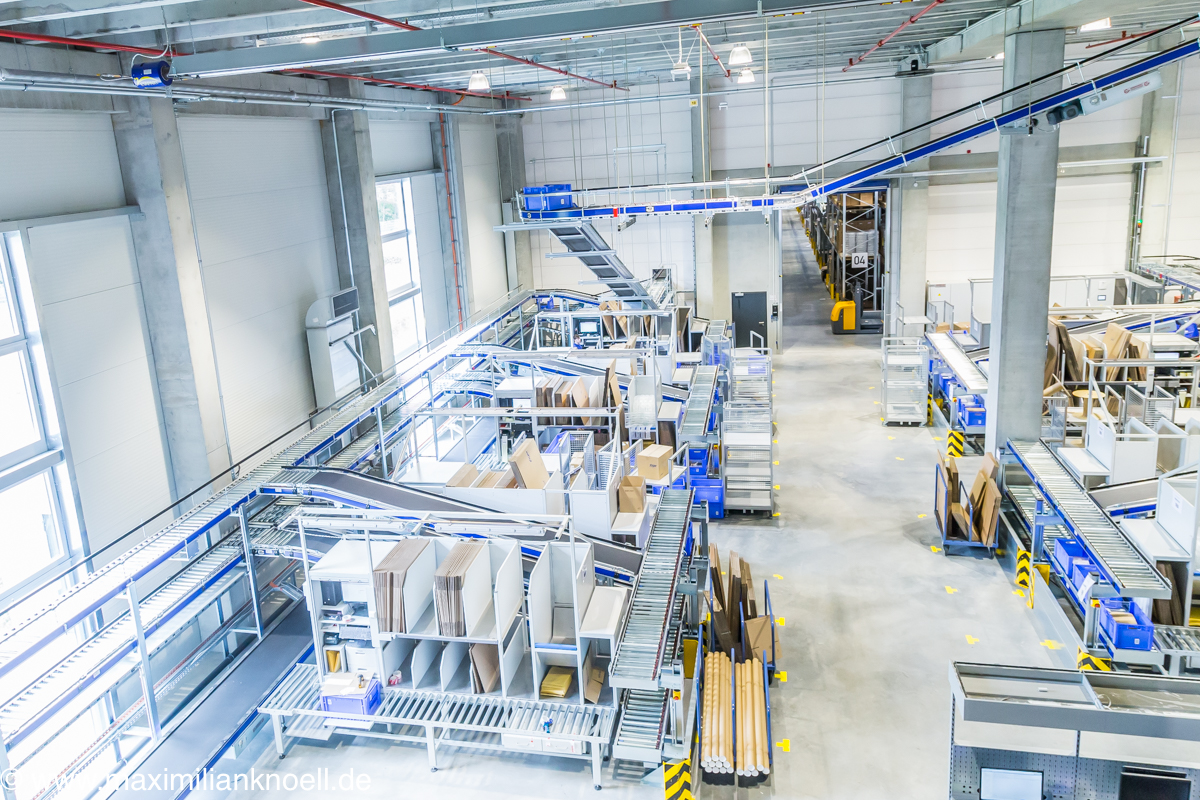
Before the production material can be processed further, it is received at goods receipt and buffered as stock in the warehouse and stored as data in the WMS. If production requires material, material provision from the warehouse is triggered via a production order from the ERP system. The required goods are reserved by the WMS SuPCIS-L8 after scheduling and sequence formation, picked by the employees and made available at the production workstations. The goods coming from production are then recorded in the WMS via a notification. Depending on whether it is customer-related goods or a larger quantity of stock goods has been produced, the goods are processed accordingly in the warehouse. Dashboards and cockpits on large screens in the warehouse and production areas help to integrate people into the largely digitized and automated processes.
Steady growth means breaking new ground
The move to the new warehouse complex at the Heppenheim site and the introduction of the SuPCIS-L8 warehouse management software from S&P represent a successful overall solution for the company. Due to the flexibility, scalability and available interfaces of the warehouse management software, the company will also have the possibility to further expand its warehouse logistics in the future and to be able to react satisfactorily to the wishes of its customers.