With the planning and implementation of one of Europe's largest AutoStore systems and coordinated process control using the SuPCIS-L8 software from subsidiary S&P, system integrator Element Logic has further developed the expansion of the goods service center of fashion and lifestyle company Breuninger.
Founded in 1881, the fashion and lifestyle company E. Breuninger GmbH & Co. is one of the leading omnichannel department stores in Europe. The company operates 13 stores in Germany and Luxembourg. It also has an online store that is available in ten European countries. The fashion, beauty and lifestyle articles are stored and dispatched for stationary retail and end customers at the Breuninger Goods Service Center (WDZ) in Sachsenheim near Stuttgart. As Breuninger has successively opened up new markets in recent years and the online store has further accelerated the company's growth, the company had to develop new capacities in the areas of warehousing, shipping, outgoing goods and returns. To this end, the approximately 76,000 square meters of gross floor space of the WDZ, which opened in 2019, was expanded by an additional hall with around 40,000 square meters.
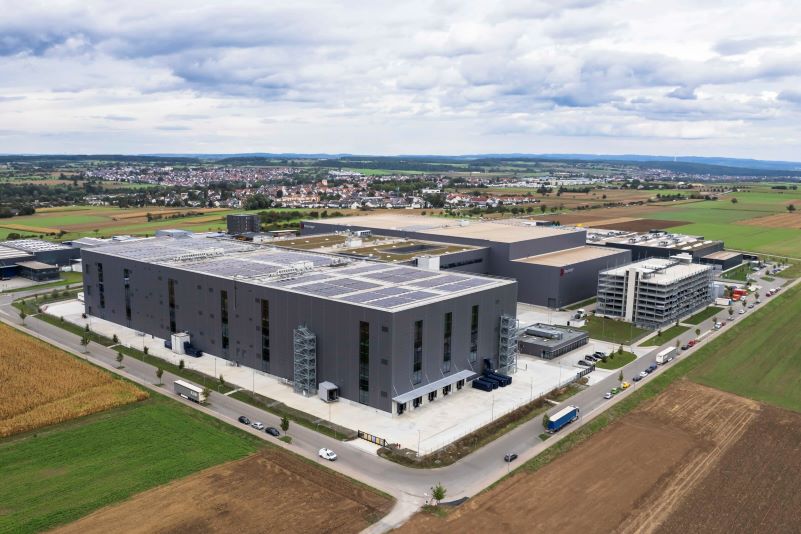
One of the largest AutoStore facilities in Europe
The expansion optimizes processes with state-of-the-art intralogistics and shortens throughput times in the Breuninger WDZ while bundling capacities at the same time. The technical highlight of the new hall is the implementation of one of the largest AutoStore systems currently available in Europe. Breuninger awarded the contract to plan and implement the system to system integrator Element Logic, the world's first AutoStore integrator. "Automation with AutoStore technology offers significant advantages in terms of performance and adaptability, especially for article storage and picking in omnichannel business and e-commerce," emphasizes Joachim Kieninger, Director Strategic Business Development Element Logic Germany. "In addition, the energy requirement is extremely low, meaning that the technology also scores highly in terms of sustainability requirements for users in the future."
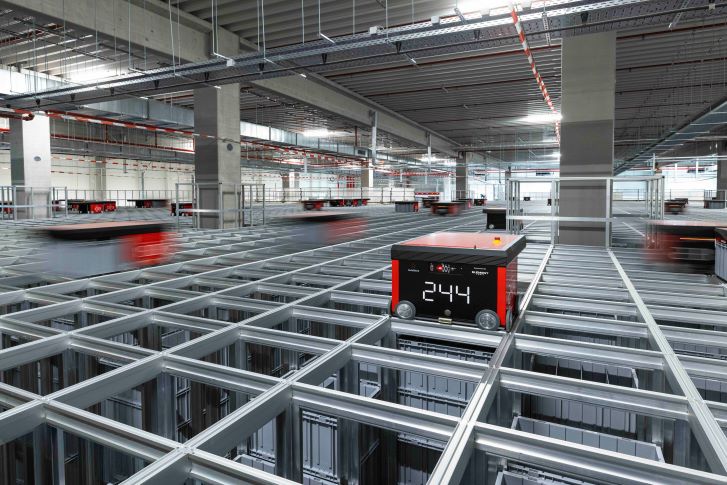
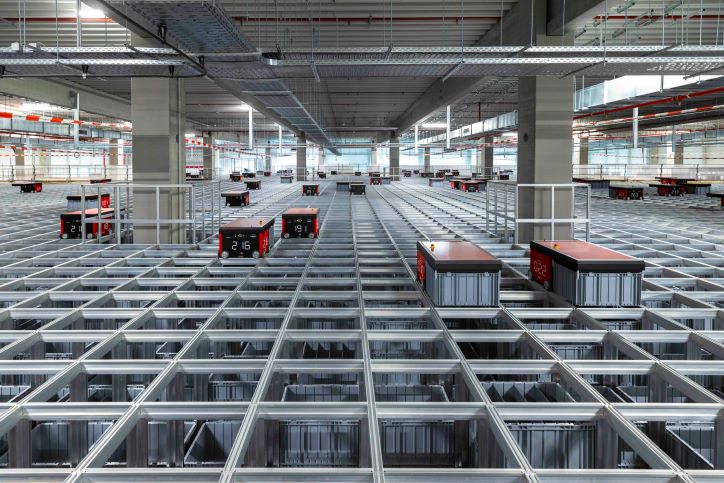
Two system blocks in two fire protection areas
Element Logic designed an AutoStore system for the expansion of Breuninger's service center, which, with its enormous dimensions, already extends across two fire protection areas in the first implementation phase. In the shafts of the two aluminum grids, which are connected by three fire doors, the system offers more than 200,000 container storage spaces on a total of 5,400 square meters of storage space. For the rapid realization of expansion projects, the plant layout already provides for a future third plant block for an upcoming expansion stage. If performance or capacity requirements increase, the system can be easily expanded by adding additional shafts and storage locations or robots and ports - a fundamental principle of AutoStore technology.
System technology components on two building levels
The 330 millimeter high system containers are stacked up to 16 high in the shafts. A total of almost 300 small robots work on the grid surface. During storage, they stack the filled system containers in the shafts, transfer them and deliver them to the work stations installed as components of the overall AutoStore system, the so-called ports, for order picking. Element Logic has installed a total of 35 of these workstations on the AutoStore for loading the system and picking the order items. Of these, 23 so-called carousel ports are designed for higher warehouse throughputs. They are mainly used for order picking. The 12 other ports, known as conveyor ports for lower throughputs, are largely used to load the system containers with incoming goods. A special feature is that the ports are integrated into the system as free-standing units, enabling the simple integration of infeed and outfeed conveyor technology at the workstations on the AutoStore. "An optimum separation of the storage cube with the ports, material flows and process areas was achieved," explains Kieninger. "The storage cube with the ports is installed on the 3rd floor."
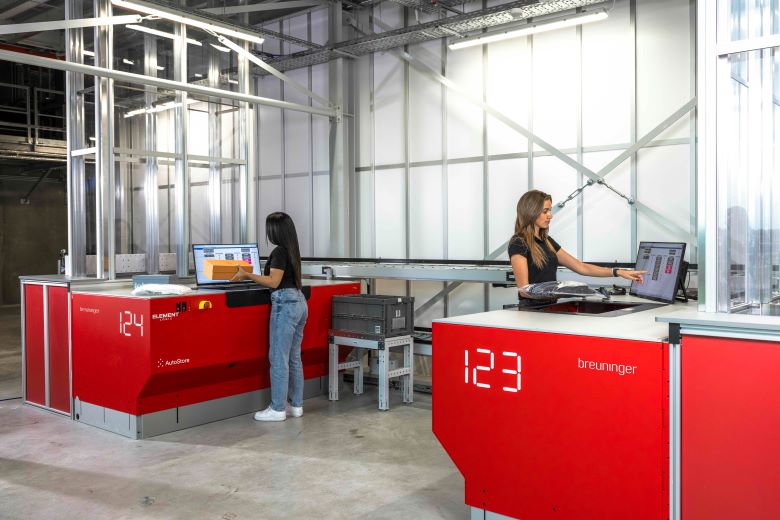
Double-decker conveyor system for container management
A two-storey conveyor system supplies the Caroussel ports on the upper level with empty containers and disposes of the filled target containers on the lower level in the direction of dispatch. Parallel to the AutoStore project planning by Element Logic, Breuninger commissioned Element Logic's subsidiary S&P to implement the SuPCIS-L8 software to control the complex processes. As a subsystem of the existing warehouse management software, SuPCIS-L8 handles inventory management and the workstation dialogs at the ports. The software optimizes the AutoStore processes and offers prioritization strategies for pending tasks. Using a standardized interface, the AutoStore Connector, SuPCIS-L8 also integrates the AutoStore system with real-time data exchange directly into the coordinated process control in the warehouse. SuPCIS-L8 also offers a number of features specially designed for AutoStore. Container management, for example, is designed to manage multi-SKUs in order to optimize stock levels. This means that goods from several containers can be combined into one container and thus compacted, or goods from one container can be divided into several containers, i.e. separated. In this way, Breuninger can not only store mixed goods in one bin, but can also fill each compartment of a 4-compartment bin with different items and specify special restrictions. This means, for example, that half-empty bins can be completely filled during storage. Fill level monitoring shows how many bins are still completely empty or still have empty partial compartments.
Single sign-on solution for employee logon
Other software features reduce the administrative and operational workload for employees. For example, a single sign-on solution allows employees to log in to SuPCIS-L8 at the same time as they log in to Microsoft. This eliminates the need for separate user names and passwords. For operational handling, employees at the ports can communicate directly with the AutoStore system via a dialog in SuPCIS-L8 without having to switch to a different control system. In addition, certain order types can be assigned to individual ports. "The automated warehouse processes in AutoStore have made the processes in the WDZ more efficient and ensured even greater precision," summarizes Kieninger. "Breuninger has thus further optimized its intralogistics and is sustainably prepared for the requirements of a dynamic market."