Rapid connection of a multi-carrier solution to the warehouse management software with maximum flexibility.
Developing an individual solution for connecting a multi-carrier shipping system usually involves a certain amount of development and implementation work. S&P Computersysteme GmbH, a manufacturer of warehouse management software from Leinfelden-Echterdingen and subsidiary of Element Logic, was looking for a more efficient solution. With its customers' concerns in mind, S&P decided to develop a standard interface for linking a shipping system to the SuPCIS-L8 warehouse management software. The solution is called the Standard Shipping Connector, or SSC for short. The SSC offers advantages for both customers and S&P by simplifying and shortening the connection of a multi-carrier solution, standardizing data exchange and significantly reducing individual development efforts.
A plug-and-play solution for all requirements
A multi-carrier solution supports companies throughout the entire shipping process and generates various shipping labels from shipping service providers, freight forwarders and carriers, among other things. In order to ensure that the relevant shipment data for the respective carrier is transferred correctly, a solution has since been individually developed with the required data from the warehouse management software. This ranged from lean variants that only transmitted the package, sender and recipient data to the transmission of complete dangerous goods data with special shipment details. Additional adaptations to the interface were required for subsequent change requests. This resulted in development and implementation costs for both sides. This problem was initially solved by the development of the SSC for the shipping system of AEB SE and Heidler Strichcode GmbH. Other systems are to follow. Thanks to the plug-and-play functionality, the two shipping systems can be integrated quickly and easily without the need for complex individual programming. Thanks to the SSC, the SuPCIS-L8 warehouse management software communicates with the shipping system in a uniform and standardized manner, regardless of which system is connected.
Enhanced flexibility with just a few clicks
With the SSC, customers benefit from the standardized provision of all necessary information from the warehouse management software. This means that all the data required for transfer to the AEB and Heidler shipping system is always available. This opens up unlimited expansion options for customers without any additional effort or adjustments to the interface. An example: If certain data was initially superfluous for generating shipping labels but will be important in the future, a quick changeover is possible. The data from the warehouse management software is available in the SSC. The additional fields required in the shipping system can be filled in with just a few clicks. "If changes are required that affect all customers, such as new country-specific processing, it is possible to make these centrally in the standard interface and import them. This ensures a high level of flexibility and efficiency," adds Rémy El Abd, Managing Director at S&P. S&P has even set up ten freely configurable fields in the SSC for individual reference numbers that customers want to see on the shipment afterwards.
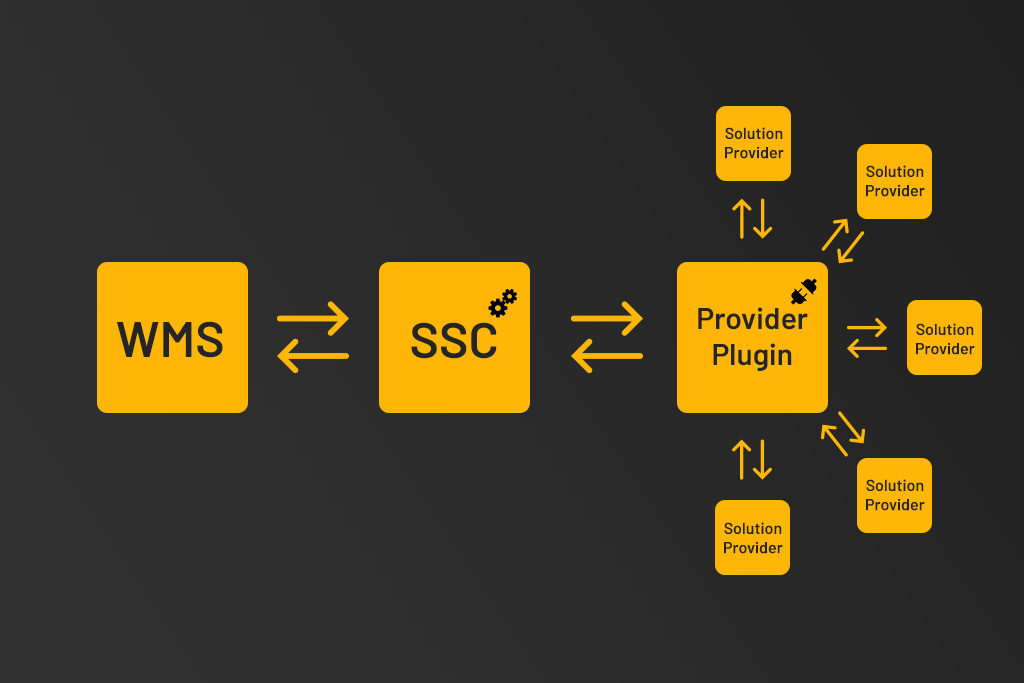
About S&P | Element Logic
S&P has been realizing software and IT system solutions for demanding logistics requirements in various industries since 1985. As a leading provider in the field of intralogistics IT, S&P is continuously developing its modular warehouse management platform SuPCIS-L8 in order to offer its customers state-of-the-art and future-proof solutions.
From consulting and optimization of business processes to commissioning, S&P offers IT solutions for all automation levels of intralogistics - from manually operated warehouses to fully automated logistics centers. In addition, S&P offers comprehensive cloud services to optimize and simplify the operation and management of customers' IT infrastructure.
As a subsidiary of Element Logic, S&P has its headquarters in Leinfelden-Echterdingen and another location in Georgsmarienhütte near Osnabrück.
Element Logic is a leading global technology company and the largest AutoStore® partner. Headquartered in Kløfta, Norway, Element Logic has locations in Europe, the USA and Latin America and achieved a total turnover of 471 million euros in 2023.
Further information can be found at www.sup-logistik.de and on our social media channels LinkedIn, Instagram and YouTube as well as at www.elementlogic.de