S&P facilitates automated warehouse operations with efficient transport coordination and a new user interface.
S&P has launched a new version of the previous component SuPCIS-DTC (Dynamic Transport Control) for the control of several automatic components that are controlled by a material flow controller (MFC). With a completely revised user interface and fully integrated into the SuPCIS-L8 warehouse management software, further developments and new releases will be less complex and less time-consuming in future. The new generation is state of the art and runs through automatic tests when changes are made. S&P relies on test-driven development with continuous reviews.
Effortless control of all transport orders
The task of SuPCIS-DTC is to receive and allocate transport orders from the warehouse management system and then pass them on to the connected automated components (e.g. to the MFC of the conveyor technology and the forklift control system). SuPCIS-DTC handles the entire transport management of the various automatic conveyor systems and means of transport. All transports to be processed are precisely coordinated and controlled. SuPCIS-DTC even takes capacity utilization or manual interventions into account when controlling the transport order. It is also easy to delete, interrupt, prioritize or postpone orders. In addition to route determination, SuPCIS-DTC also monitors the timing of transports. If transports take too long, the system alerts the control center. All movements and individual transport statuses are displayed to the control center in a dashboard. SuPCIS-DTC is fully integrated into SuPCIS-L8. The information and workstation dialogs follow the same operating principle, regardless of which manufacturer is connected. This not only simplifies the work of the S&P service team, but also that of the customer. If the customer has several locations, they can deploy staff more flexibly. Change requests can also be implemented more quickly. The system also enables the control of external MFCs. The MFC connection is standardized and can therefore be easily and quickly coordinated with the respective supplier.
Takes control and maintains an overview
SuPCIS-DTC manages routes, loading units, transport types and destinations in addition to transport orders. Another special feature: several destinations can be managed. This means that either all destinations or only certain destinations can be approached on one day. Parameters for the routes and the MFCs are set in the system. In other words, transfer points are defined for the MFCs and how they are to be connected with each other. What is an MFC and what does it actually do? The MFC is the control software of an automated system. It is used, for example, to monitor the individual conveyor technology elements of this automated system. The MFC also ensures that the system is not overloaded and that there are no jams or blockages. Back to SuPCIS-DTC. SuPCIS-DTC receives the transport orders from the warehouse management system. A transport order comprises the movement of a load unit to one or more destinations. It is considered complete when the destination or one of the specified destinations has been reached. For example, the load unit or a group of load units (batch formation) is required at a specific picking location. SuPCIS-DTC then checks where the load unit is located and whether the destination (the picking location) has sufficient capacity. If so, SuPCIS-DTC sends the load unit on its way. SuPCIS-DTC itself has no execution options, but only checks which MFC is responsible for this route section and which route is the best. If, for example, part of the conveyor system is damaged or out of order, SuPCIS-DTC suggests an alternative route. The MFC reports the completed transport back to SuPCIS-DTC and, if necessary, sends a new transport order to the next MFC until the destination is reached.
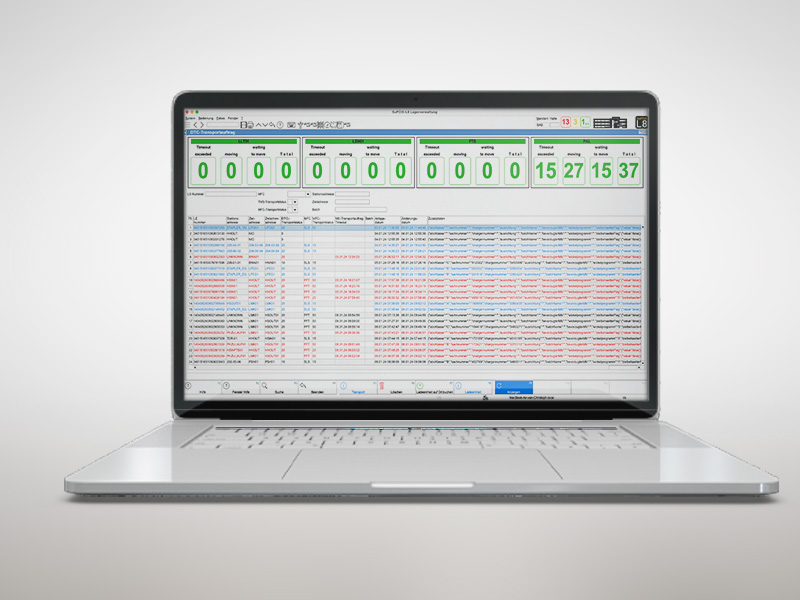
About S&P | Element Logic
S&P has been realizing software and IT system solutions for demanding logistics requirements in various industries since 1985. As a leading provider in the field of intralogistics IT, S&P is continuously developing its modular warehouse management platform SuPCIS-L8 in order to offer its customers state-of-the-art and future-proof solutions.
From consulting and optimization of business processes to commissioning, S&P offers IT solutions for all automation levels of intralogistics - from manually operated warehouses to fully automated logistics centers. In addition, S&P offers comprehensive cloud services to optimize and simplify the operation and management of customers' IT infrastructure.
As a subsidiary of Element Logic, S&P has its headquarters in Leinfelden-Echterdingen and another location in Georgsmarienhütte near Osnabrück.
Element Logic is a leading global technology company and the largest AutoStore® partner. Headquartered in Kløfta, Norway, Element Logic has locations in Europe, the USA and Latin America and achieved a total turnover of 471 million euros in 2023.
Further information can be found at www.sup-logistik.de and on our social media channels LinkedIn, Instagram and YouTube as well as at www.elementlogic.de